This article is published in Aviation Week & Space Technology and is free to read until Aug 15, 2024. If you want to read more articles from this publication, please click the link to subscribe.
Parts Removal Problems Well-Known Within Boeing Before Alaska 737-9 Accident
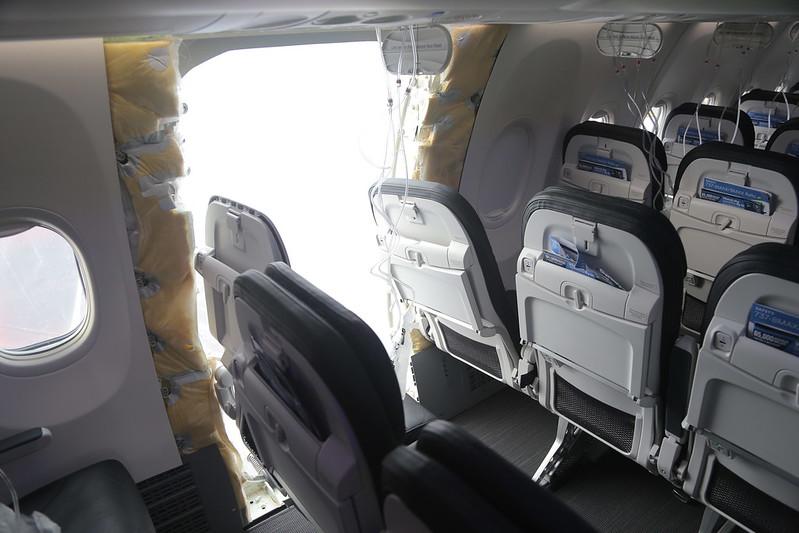
Boeing was concerned enough about compliance with parts-removal requirements to have the issue under a formal safety risk assessment when an Alaska Airlines 737-9 lost a panel that was improperly removed during production, testimony during an NTSB hearing on the January accident revealed.
Employees raised concerns about Boeing’s “Perform Part or Assembly Removal” process in March 2023 via the company’s voluntary Speak Up reporting program, Boeing safety management system (SMS) senior director Paul Wright said Aug. 7, the hearing’s second day. The company’s SMS process determined the issue required a safety risk assessment (SRA).
The SRA was in process when the Alaska 737-9 lost its left side mid-exit door (MED) plug on Jan. 5, forcing the aircraft to make an emergency landing. Nobody onboard was hurt, but the accident chain’s circumstances are prompting significant changes at Boeing and with FAA’s surveillance.
NTSB investigators have determined that four retaining bolts removed from the MED as part of a pre-delivery repair were not re-installed. The aircraft passed a number of pre-delivery inspections and flew 154 flights before the plug blew out—in part because unlike other doors, the MED plug is not designed to rely on a sensor that triggers if it is not fully secure.
Removal of the plug to repair five adjacent rivets required formal documentation in Boeing’s Common Manufacturing Execution System (CMES). None was prepared, Boeing determined. Spirit conducted the rivet repairs, but Boeing’s protocol required its employees to both prepare the removal documentation, known as Boeing Process Instruction (BPI) 1581, and handle the door.
It is not clear why the retaining bolts were not re-installed, where the hardware ended up, or who was last to touch the MED plug after the work was finished and the aircraft delivered to Alaska in October 2023.
Boeing’s recognition that a more urgent risk review process may have prevented the mistakes that led to the Alaska accident have prompted the company to change protocols.
“Having that full analysis done for the initial risk is too long,” said Wright. “So, we’ve changed our process ... The initial risk has to be placed within seven days” once the issue is added to the formal “risk register,” he continued. “We have a dedicated team overseen by myself, that does those initial placements.”
Information gathered by the NTSB shows both Boeing and the FAA were acutely aware of production-line problems with unauthorized removals well before the Alaska accident happened. Eight internal audits from 2018-2023 “found issues with unauthorized removals,” an NTSB report prepared during the investigation shows.
Concerns among production-floor workforce have prompted 35 removal-related Speak Up reports since 2019. Ten are still open.
Employees who submitted speak-ups “were concerned about how to make sure teammates had all the necessary information for the reinstallation,” said Wright. “Particularly to make sure that tests were conducted properly,” he added.
Problems with removals were linked to 16 “regulatory compliance issues” from 2018-2023, the NTSB report said. Boeing voluntarily disclosed nine of these and seven were “compliance actions” cited by the FAA, signifying unintentional mistakes that the company agreed to correct. None led to enforcement actions. Eight of the issues were 737-related, but none involved MED plugs.
“We did identify this issue,” said Brian Knaup, an FAA manager with direct Boeing certificate oversight responsibility. “We worked through our compliance actions and tried to ensure Boeing implemented corrective actions around this issue—the reinstallation of parts and ensuring that the [installation plans] were adequate.
“The removal process ... is a very complex process,” he added. “We did attack that process.”
An FAA audit conducted after the Alaska accident found still more removal-related issues that may lead to FAA penalties.
“We have open enforcement actions currently,” Knaup said. ”It is an open investigation.”
Boeing has determined that frequent updates of BPI 1581 are not being adequately communicated to employees. The company made 11 “notable” updates to BPI 1581 from 2013-2023 prompted by a variety of sources, including internal audit findings and “commitments to the FAA,” the NTSB document said.
Boeing said it plans to make less frequent updates to BPI 1581 and has instituted training that covers when and why removal documentation is required. Its CMES has been updated to prevent employees from conducting removals unless they have undergone the training.
More planned improvements are included in a 90-day corrective action plan Boeing submitted to the FAA following the most recent audit.